Effective stock replenishment: How and why?
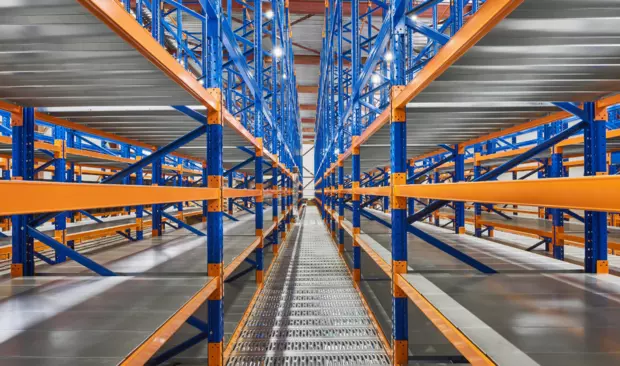
The power of stock replenishment in warehouse management
Knowing exactly what stock is moving in and out of your warehouse is a cornerstone of successful operations. However, a surprising number of businesses still grapple with inadequate visibility and control over their stock replenishment levels. This gap in management can lead to a ripple effect of inefficiencies and missed opportunities.
Why stock replenishment matters
✅ Accurate stock levels
At the heart of any warehouse management system (WMS) is the ability to maintain accurate stock levels. This precision is not just about knowing how much of a product is available but also understanding the dynamics of supply and demand. Accurate stock levels ensure that businesses can meet customer demands without overstocking, which can tie up capital unnecessarily.
✅ Enhanced warehouse efficiency
Efficient warehouse operations hinge on the smooth flow of goods. When stock replenishment is well-managed, it minimises the time and resources spent in handling inventory. This efficiency translates into quicker turnaround times, reducing warehouse costs and improving overall productivity.
✅ Improved order fulfilment and customer service
A direct offshoot of efficient stock management is the ability to fulfil orders promptly and accurately. In today’s fast-paced market, customers expect quick deliveries. A robust replenishment system ensures that products are always available for picking, thereby enhancing customer satisfaction and loyalty.
✅ Sustainability
In the broader context, effective stock replenishment contributes significantly to sustainability. By avoiding overstocking, businesses reduce waste and manage resources more responsibly. This approach not only supports environmental sustainability but also aligns with the growing consumer preference for eco-friendly business practices.
The role of technology in stock replenishment
Stock replenishment is crucial for maintaining fast order dispatch. A common mistake in warehouses is to put goods away in bulk stock locations or high racking first, instead of prioritising replenishment bins and pick faces. This leads to double handling of stock, as another warehouse operative later moves these goods into replenishment bins or pick faces. This not only creates elongated processes but also affects warehouse productivity and dispatch efficiency.
To avoid these pitfalls, including stock replenishments as part of goods put away procedures is essential. This is where the Orderwise Stock Replenishments module comes in. It offers an organised method of managing replenishment from bulk stock locations and is compatible with both the main OrderWise system and Mobile Warehouse Management (WMS) Devices. It efficiently guides pickers via the best walk route to collect stock before replenishing into the relevant bins, thereby maximising warehouse productivity.
Consumer insights and impacts
The impact of efficient stock replenishment extends beyond the warehouse. Consumer behavior studies have shown that:
- Approximately 30% of consumers feel that stockouts negatively impact their shopping experience.
- Around 69% of customers will opt for a substitute item after encountering a stockout for the first time.
- A staggering 70% are likely to switch brands entirely after experiencing repeated stockouts.
Stockouts, or situations where products are unavailable, have a profoundly negative impact on customers. They lead to immediate dissatisfaction and inconvenience, as customers are unable to purchase the desired item. This disappointment is compounded when the item is needed urgently, leaving the customer in a lurch.
Furthermore, stockouts can damage the customer's perception of a brand. When customers consistently encounter unavailable products, they may perceive the brand as unreliable or poorly managed, eroding trust and confidence in the company. This is especially detrimental in an era where customer loyalty is hard-won and easily lost.
Stockouts also force customers to seek alternatives, often leading them to competitors. This not only results in lost sales in the short term but can also lead to a long-term shift in customer loyalty. Once customers find a reliable alternative, they may not return, even after the original item is restocked.
Level up your stock control
Effective stock replenishment isn't just a component of warehouse management; it’s a pivotal factor in the broader spectrum of business operations. From ensuring accurate stock levels to enhancing customer satisfaction and supporting sustainability, the benefits of a well-managed stock replenishment system are manifold.
As technology continues to evolve, it presents an opportunity for businesses to refine their replenishment strategies further, aligning them with the demands of an ever-changing market.
Discover more about WMS technology
Ready to transform your warehouse? Discover how the right solution can elevate your business to new heights. Say goodbye to stockouts and hello to a warehouse where every aspect of your inventory is managed with precision.
Evolve your Orderwise WMS solution
Already a part of the Orderwise community? Perhaps it's time to take your warehouse efficiency to the next level? Incorporate stock replenishment into your existing system and witness a transformation in your stock control.